Using turbidity sensors to optimize filter backwashing
In rapid gravity filtration (RGF) systems, backwashing is a critical process—it removes accumulated solids from the filter bed to prolong filter life and maintain safe, high-quality water. Relying on timers to control the process often leads to over- or under-washing, wasting valuable potable water and energy, or leaving filters inadequately cleaned.1
Real-time turbidity sensors offer a better approach. By measuring water clarity in real time, operators can clean filters precisely when needed and stop the process as soon as it’s effective.
The importance of filter backwashing
Backwashing is essential to maintain filter performance. As particles and contaminants accumulate in the filter bed, periodic cleaning is required to restore flow and ensure water quality. Backwashing reverses the flow of water through the filter to dislodge and remove trapped solids, preparing the filter for the next cycle.
A typical backwash sequence includes:
- Remove the filter from service
- Air scour with high-velocity air to dislodge particles from the filter media, loosen debris, and prepare the filter for the following stages.
- Reduced-flow backwash with a lower flow rate water to gently flush out dislodged particles and ensure the filter media remains undisturbed.
- Full-flow backwash with higher flow rate water to thoroughly rinse the filter, ensuring all particles are flushed away.
- Ripening period after backwash, where the filter sits to re-establish a natural surface layer before returning to service.
Operating these cycles based solely on time presents two risks: under-washing and over-washing. Over-washing wastes potable water and energy and can cause filter media loss. Under-washing leads to shorter run-times, clogged filters, and poor effluent quality due to solids build-up and media migration. 2
Turbidity provides a reliable way to determine when to end the backwash process.
Using turbidity sensors for smarter backwashing
Turbidity is a key water quality parameter in drinking water treatment, indicating the concentration of suspended solids. During backwash, it directly indicates how effective the cleaning process is in real time.3
Turbidity can be measured at three main points around the filter bed:
- In the filter bed itself. This is the simplest installation, but turbulence and entrained air during backwash can scatter the light beam used by turbidity sensors. For best accuracy, the sensor should be positioned just above the media to reduce bubble interference. A limitation of this location is that it only reflects conditions at one fixed point in the filter.
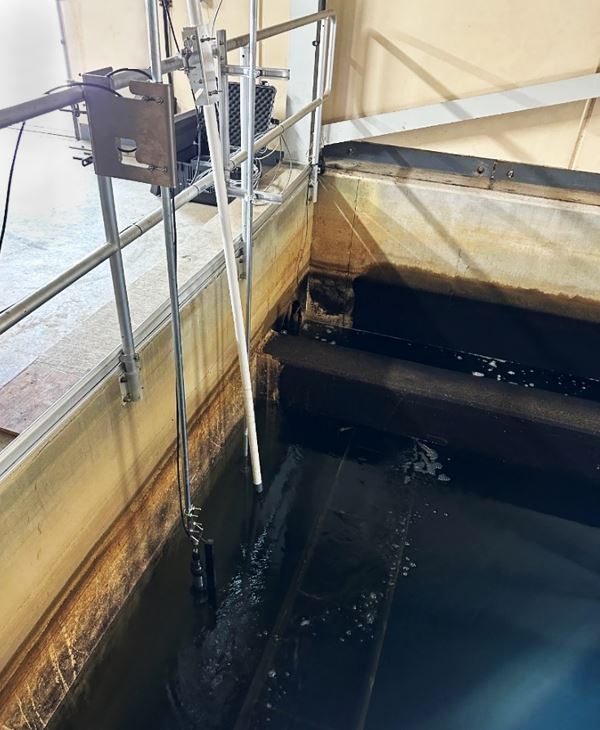
Figure 1: VisoTurb 700 IQ sensor in a filter bed. This location provides an easy installation and turbidity provides an accurate measurement when the sensor is installed just above the filter media.
- In the wash-water trough. Located at the top of the filter bed and discharging backwash water, this location provides a more representative sample of the entire bed. However, installation can be more difficult depending on the trough design. Sensors like the VisoTurb 700 must be placed at least 10 cm (4 in.) from surfaces.
Figure 2: A wash-water trough at the top of the filter bed. Sensor placement here provides a more representative turbidity reading but must account for installation constraints.
- In the combined backwash outlet channel. This provides the most stable and representative measurement, with minimal turbulence or aeration. However, it can be challenging to access. A SCADA system with a filter-specific lag time is required to align measurements with the correct filter. Since filters are typically backwashed one at a time, this lag adjustment is straightforward to implement.
The U.S. EPA, referencing AWWA guidelines, recommends terminating the backwash process once turbidity has dropped to between 15-20 NTU.3 Relying on this threshold—rather than an arbitrary time value—helps optimize performance, minimize water loss, and improve filter readiness for the next cycle.
Example: Real-world optimization
At one example site, the backwash process follows this sequence:
- Filter Operation/Run-Time: 72 Hours
- Air Scour: 3 minutes at 600 scfm
- Reduced backwash: 3 minutes at 2,300 gpm
- Full flow backwash: 10 minutes at 2,650 gpm
Turbidity levels spike to 90 FNU during air scour at the beginning of the backwash cycle.
Figure 3: Example RGF Air Scour Turbidity
Turbidity levels gradually decrease during rinsing. After four minutes, turbidity plateaus around 10 FNU—the target setpoint for ending the backwash. However, the process continues for another seven minutes, during which no further turbidity improvement occurs.
Figure 4: Turbidity Levels during backwash rinse
The excess backwashing wastes 18,640 gallons per cycle. Over 122 cycles per year, this adds up to more than 2.2 million gallons of clean water lost—just from one filter.
Advanced turbidity sensor technology
Accurate turbidity readings depend on clean optical windows. Traditional sensors use mechanical wipers to clean these surfaces, but over time, moving parts can fail and require maintenance.
The VisoTurb 700 IQ uses integral ultrasonic cleaning instead—vibrating at high frequencies to prevent fouling without mechanical parts. This reduces maintenance needs and improves long-term reliability.
Figure 5: VisoTurb 700 IQ with ultrasonic self-cleaning. High-frequency vibration keeps optical surfaces clear without the use of mechanical wipes.
Conclusion
Turbidity sensors offer direct, real-time insight into the effectiveness of filter backwashing. With smarter control, operators can reduce water waste, protect equipment, and improve overall treatment performance. Upgrading to advanced sensors like the VisoTurb 700 IQ is a simple step that delivers lasting impact. If you’re looking to optimize your backwash process or have questions about turbidity sensor installation, connect with our team—we’re here to provide expertise and help you get the most from your system.
Sources:
- National Environmental Services Center, Filter Backwashing
- International Water Association, Rapid Gravity Filtration: Water Quality Benefits and Risks
- U.S. Environmental Protection Agency, Surface Water Treatment Rule Turbidity Guidance Manual